Design of a dynamic vibration absorber for a machining center
Depending on the tool position, high vibration magnitudes were observed at the spindle of a machining centre. These vibrations are caused by resonances which are excited by the residual unbalance of the spindle and the operation of the tool.
The top figure shows the FEA model which was correlated with vibration measurements. The vibration magnitude of the spindle at operation speed was significantly reduced by local stiffening measures.
The vibration magnitudes were further reduced by developing two independent dynamic vibration absorbers, one for the cross-slide and one for the z-slide of the machining centre, respectively.
The modal data of the machining centre were exported to MATLAB/Simulink in order to apply efficient optimizing algorithms.
First of all, an optimal position of the dynamic vibration absorber was determined taking into account the mechanical feasibility of the construction. Subsequently, the optimal values for the mass, the stiffness and the damping of the dynamic vibration absorber were determined by parameter variation.
As an example, the mid figure shows the development of the maximum dynamic compliance at the spindle tip when varying the mass and the stiffness of the dynamic vibration absorber. With increasing mass the optimal stiffness of the dynamic vibration absorber is increasing disproportionately.
Despite of the already high damping observed for the relevant resonances, a magnitude reduction of about 45% for the first resonance and about 25% for the second resonance, respectively, could be achieved. This was proven by measurements as shown in the bottom figure.
Our specialists are always at your disposal to flexibly respond to your respective requirements and wishes.
Dr. Michael Elbs, Managing Director
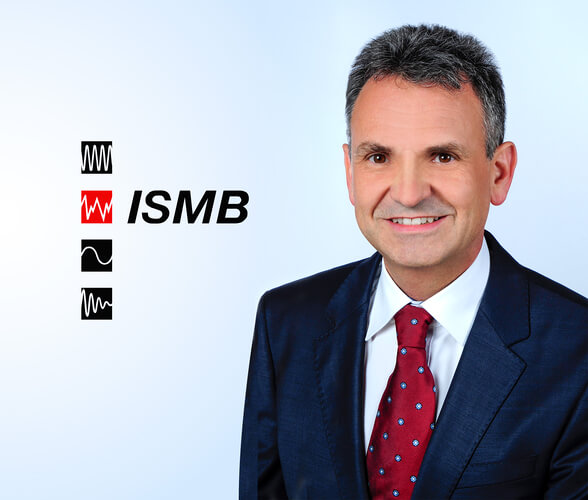
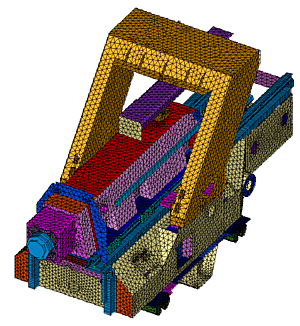
FEA model of the machining centre

Design of the absorber: maximum dynamic compliance depending on mass and stiffness of the absorber
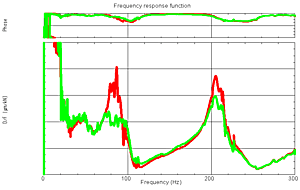
Measured frequency response function at the spindle tip without absorber and using both absorbers