Content
FEA simulation: product development and troubleshooting with high-tech and expertise
Content
You too can optimize your products with the help of FEA services from ISMB. Our experienced engineers use state-of-the-art simulation methods to analyze the mechanical, vibration, acoustic, thermal, and fluidic behavior of your components, machines, units, and systems. The simulation results can be used to reliably identify possible weak points and sources of error and to derive optimization potential for your products. From troubleshooting and increasing reliability to function optimization, weight savings and cost reduction, we support you in the sustainable improvement of your products and new developments. Our FEA calculation office offers customized FEA analyses for all industries.
FEA simulations form an essential basis for successful product development and product optimization. With ISMB, you can rely on a renowned service provider for FEA in Germany, which is characterized by a high level of expertise and flexibility. Our experienced team of engineers will respond to your individual requirements and develop the optimum solution for your project.
FEA simulations form an essential basis for successful product development and product optimization. With ISMB, you can rely on a renowned service provider for FEA in Germany, which is characterized by a high level of expertise and flexibility. Our experienced team of engineers will respond to your individual requirements and develop the optimum solution for your project.
FEA simulation as a service: Overview
Avoid weak points and reduce costs: an FEA analysis with ISMB is worthwhile
Depending on the industry and application, your products must meet quite different requirements. FEA analysis makes it possible to reliably assess the static, vibration, acoustic and thermal properties of components, machines, units, and systems at an early stage of development. Typical questions in this context are, for example:
- Will a component withstand the static, dynamic and thermal loads to be expected according to the load specifications?
- Are the expected vibration amplitudes below the specified limit values?
- Will the deformations of a component remain within the permissible range?
- What causes the strong vibrations of a machine observed during operation and how can these be reduced?
- How can the service life of a critical component be increased in order to reliably avoid fatigue fractures?
- How can a component be designed and manufactured in a way that saves material and costs while maintaining the same service life?
- How can thermal power loss be dissipated to the environment as effectively as possible?
- What is the cause of the conspicuous or disturbing noise behavior of a machine?
- How can the noise emission of a machine be reduced?
As an FEA service provider, we answer these and similar questions on the basis of careful analysis and our more than 25 years of experience from a wide range of projects and industries. We simulate the behavior of your product under typical and, if necessary, extreme loads and boundary conditions. Possible weak points can thus be reliably identified and appropriate optimization measures introduced. We use suitable validation procedures to ensure that the results of the simulation reliably match reality. If required, we can also carry out vibration measurements on your product.
The earlier you incorporate the valuable findings of an FEA analysis into your development and production process, the faster you will achieve market and application readiness for your products. By simulating a wide range of loads and influences, you can draw crucial conclusions to make your product safer, more efficient and more durable. This is not only a competitive advantage, but also important protection against the threat of warranty claims or claims for damages.
The earlier you incorporate the valuable findings of an FEA analysis into your development and production process, the faster you will achieve market and application readiness for your products. By simulating a wide range of loads and influences, you can draw crucial conclusions to make your product safer, more efficient and more durable. This is not only a competitive advantage, but also important protection against the threat of warranty claims or claims for damages.
FEA simulation disciplines
The right method for every project
The term FEA simulation stands for a whole range of numerical analysis methods for different physical tasks. The common idea of the finite element method is to break down geometrically complex calculation areas into many simple sub-areas, the finite elements. Depending on the physical problem, this results in quite different systems of differential equations, which are solved using customized numerical methods. The FEA methods used by ISMB are briefly presented below.
Static FEA analysis
In FEA static analyses, the behavior of components or assemblies is examined under specified static or quasi-static loads. These can be, for example, external forces and moments that are constant over time or change only slowly, compressive loads, dead weight, wind loads, acceleration loads or temperature stresses. The static FEA analysis includes the following sub-areas:
Strength verification with FEA:
How robust are your products?
Using static FEA analyses, the global and local component stresses of critical components are determined under the expected static, quasi-static, dynamic, and thermal loads and evaluated according to industry-specific standards or the cross-industry FKM guideline “Computational strength verification for machine components”. Typical results are degrees of utilization, the number of load cycles that can be sustained and the expected service life. If necessary, design optimization measures are developed from the results of the FEA analysis in close consultation with the customer.
Depending on the complexity of the task, the local stress distributions are determined using linear or non-linear static FEA, if necessary, taking into account contact conditions, non-linear material behavior and large deformations. Non-linear FEA analyses with linear elastic-ideal plastic or real material behavior are carried out to exploit plastic load-bearing reserves. Depending on the type of load, the buckling and buckling stability is also verified.
Depending on the complexity of the task, the local stress distributions are determined using linear or non-linear static FEA, if necessary, taking into account contact conditions, non-linear material behavior and large deformations. Non-linear FEA analyses with linear elastic-ideal plastic or real material behavior are carried out to exploit plastic load-bearing reserves. Depending on the type of load, the buckling and buckling stability is also verified.
Deformation analysis:
Are your products resistant?
- Do the deformations on the sealing surface remain so small even at maximum operating pressure that they can be compensated by the seal?
- How large are the relative displacements between the tool and the workpiece due to the dead weight load in a machining center?
- How large is the deflection of a support arm at maximum operating load and how can collisions with the feed system be avoided?
- How much do the bearing blocks of an industrial gearbox tilt at maximum torque and how must the gearing be corrected to ensure the most uniform contact pattern possible?
These and similar questions can be answered with an FEA-based deformation analysis. Depending on the task, we use linear or non-linear static FEA simulations.
We are happy to support you.
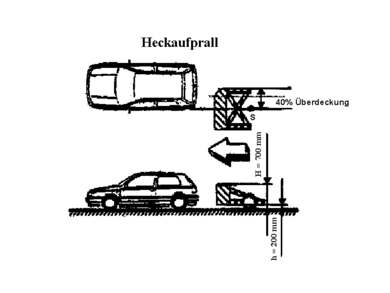
learn morePDF
Welding seam simulation FEA / Screw connections FEA:
How strong are component joints?
The connections between components such as weld seams and bolted connections are often the weak points in structures. With the help of linear and non-linear static FEA analyses, we determine the stresses on welded joints and bolted connections and carry out the necessary strength verifications.
Depending on the task, we carry out the weld seam verification, e.g. in accordance with the FKM guideline “Computational strength verification for machine components”, according to the nominal stress concept, the structural stress concept (hot-spot concept according to IIW with surface extrapolation or internal linearization) or the notch stress concept (e.g. R1MS method). We often use a substructure technique in which detailed models of critical weld seam areas are integrated into the overall model or the results of an overall simulation are transferred as boundary conditions to the cut surfaces of submodels.
For the verification of bolted joints, the bolt forces and torques are usually evaluated in the FEA model and assessed in accordance with the relevant standards. Alternatively, detailed simulations are carried out using the substructure technique.
Depending on the task, we carry out the weld seam verification, e.g. in accordance with the FKM guideline “Computational strength verification for machine components”, according to the nominal stress concept, the structural stress concept (hot-spot concept according to IIW with surface extrapolation or internal linearization) or the notch stress concept (e.g. R1MS method). We often use a substructure technique in which detailed models of critical weld seam areas are integrated into the overall model or the results of an overall simulation are transferred as boundary conditions to the cut surfaces of submodels.
For the verification of bolted joints, the bolt forces and torques are usually evaluated in the FEA model and assessed in accordance with the relevant standards. Alternatively, detailed simulations are carried out using the substructure technique.
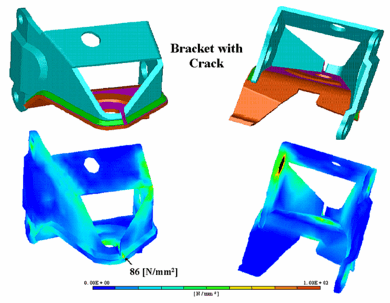
learn morePDF
Free Consultation
Our specialists are always at your disposal to flexibly respond to your respective requirements and wishes.
Dr. Michael Elbs, Managing Director
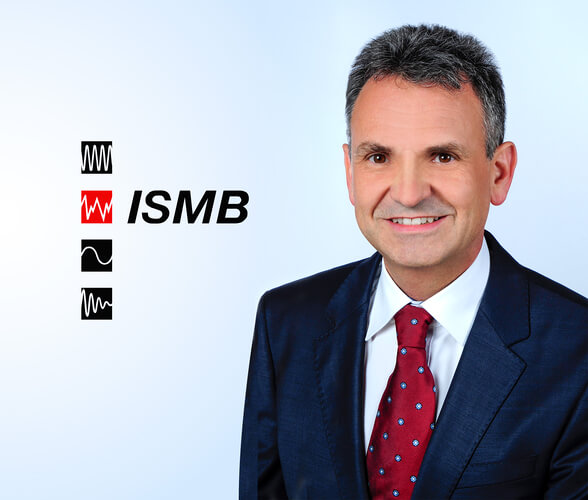
Dynamic FEA analysis / vibration analysis
We use various vibration analysis methods to investigate the vibration behavior of machines, units, and systems. Dynamic, vibrating systems can be caused to vibrate by time-varying, alternating, or pulsating, internal or external forces and torques, but also by mechanisms. With the knowledge gained from dynamic FEA analyses, you can effectively counteract disruptive vibrations and the resulting noise and fatigue. Our vibration analyses are individually tailored to your task. This enables us to derive precise statements about the vibration behavior of your product, possible weak points and targeted countermeasures.
Rotor dynamics FEA simulation:
Vibration analysis of fast rotating machines
High-speed rotating components, e.g. in turbomachinery or centrifuges, can be subject to considerable centrifugal forces, unbalanced forces, and gyroscopic forces. Rotor dynamics describes the vibration behavior of such drive trains and systems. As part of rotor dynamics simulations, we investigate the rotor dynamic vibration behavior of your rotating components and machines. Among other things, we create frequency maps for the speed-dependent natural frequencies in Campbell representation and simulate the vibration response for specified balancing qualities. Critical, rotordynamic natural vibration modes such as synchronization modes as well as the operating vibration modes in continuous resonances and stationary operating points are displayed as animations. We collaborate with you to develop measures for the safe rotordynamic design of your drivetrains.
Our engineering office for FEA calculations supports you both in the design phase and in the optimization of existing systems.
Our engineering office for FEA calculations supports you both in the design phase and in the optimization of existing systems.
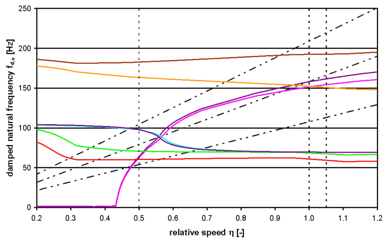
learn morePDF
Multi-body simulation:
How do parts of a system move in relation to each other?
Multi-body simulation (MBS) is used to analyze systems that consist of several rigid or flexible bodies that are coupled together via kinematic connections such as joints, bearings, or guides. Our services in this area include the following points:
- Dynamics of flexible multi-body systems / Elastic multi-body systems
- Rigid body dynamics
- Mechanisms with transient or geometrically non-linear movements
The multi-body simulation provides detailed information about motion sequences (paths, angles, speeds, accelerations), resulting forces and moments as well as resulting stresses and the transient contact conditions between components.
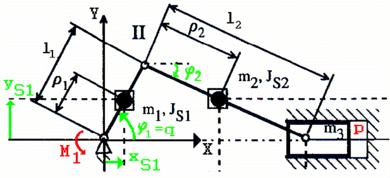
learn morePDF
Operating vibrations:
What to do about unwanted vibrations?
The vibrations that occur during machine operation can not only lead to disruptive noise or breakdowns but can also pose a safety risk. It is therefore advisable to simulate the vibration behavior of machines, units and systems using FEA as early as the design phase so that design measures can be taken at an early stage if necessary.
Vibration analyses on machines or vibration analyses on motors enable detailed predictions to be made about the vibration behavior during subsequent operation. With the help of FEA simulation, we make reliable predictions about linear and non-linear vibrations and develop suitable solutions for vibration reduction.
In addition to computational operational vibration analysis with FEA, we are also your partner for vibration measurements in Germany and worldwide.
Vibration analyses on machines or vibration analyses on motors enable detailed predictions to be made about the vibration behavior during subsequent operation. With the help of FEA simulation, we make reliable predictions about linear and non-linear vibrations and develop suitable solutions for vibration reduction.
In addition to computational operational vibration analysis with FEA, we are also your partner for vibration measurements in Germany and worldwide.
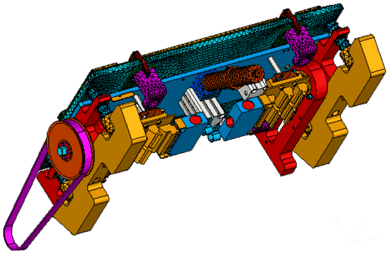
learn morePDF
Fatigue strength:
How reliable are machines against vibrations?
FEA analyses of fatigue strength (structural analysis) can be used to determine the expected service life of components, assemblies, and overall systems under vibration load. Both typical, “normal” operating conditions and rarely occurring operating conditions are considered and weighted accordingly. It is important to reliably predict the essential system natural frequencies using an FEA model that is set up appropriately for vibration and, if possible, correlated with experimental modal data. Furthermore, the main excitation mechanisms must be known. These are often internal forces such as imbalances, pressure pulsations or electromagnetic forces or external excitations, which can be described by base point excitations on flange planes. The dynamic stresses determined using a linear or non-linear FEA vibration analysis are evaluated against material parameters such as fatigue strength, fatigue strength, fatigue strength, fatigue strength in bending, swelling strength and fatigue strength.
Have the fatigue strength of your products evaluated with an FEA fatigue strength analysis. Use the information obtained in this way to significantly increase the service life of your components and systems. In accordance with the FKM guideline, we prepare static and dynamic strength verifications, strength verifications for welded joints and fatigue strength verifications for you.
Have the fatigue strength of your products evaluated with an FEA fatigue strength analysis. Use the information obtained in this way to significantly increase the service life of your components and systems. In accordance with the FKM guideline, we prepare static and dynamic strength verifications, strength verifications for welded joints and fatigue strength verifications for you.
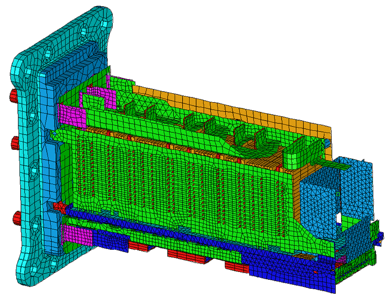
learn morePDF
FEA modal analysis:
How can resonance vibrations be avoided?
In addition to the operational vibration analysis, which describes the vibration behavior in real operation, the computational FEA modal analysis (FEA Modal Analysis) determines the natural frequencies and natural vibration modes of components, assemblies, and systems. These modal parameters represent essential system properties, knowledge of which can be used to optimize the vibration behavior of your products. Resonance vibrations and thus unacceptably high vibration amplitudes and component loads can be reliably avoided by ensuring a sufficient distance between the essential natural frequencies and the relevant operating frequency range. An important example of this is drive shafts, where the bending natural frequencies must have a sufficient distance to the operating rotational frequency. The same applies to torsional natural frequencies in the case of rotational excitation, e.g. due to the timing of compressors or combustion engines.
In addition to numerical modal analysis using FEA simulation, we also offer experimental modal analysis. Please contact us.
In addition to numerical modal analysis using FEA simulation, we also offer experimental modal analysis. Please contact us.
Acoustics
The acoustic behavior of products plays an important role in many industries. This primarily involves compliance with the immission limit values for the respective location, occupational health and safety requirements and spectral level requirements that are agreed in specifications. In addition to high overall levels, significantly quieter noises can also be perceived by people as very unpleasant and disturbing if they have an “unusual” noise signature, such as knocking noises, screeching, or squeaking noises, beats, high-frequency individual tones, etc.
Acoustic simulations and acoustic measurements therefore play an important role in many industries. Acoustic analyses are an effective means of counteracting unnecessary or excessive noise development. An FEA acoustic analysis helps you to understand the sound emissions of your products and to reduce them in a targeted manner. We simulate and optimize the sound emission of your products using FEA simulation, taking into account fluid-structure coupling, the interaction of airborne sound and structure-borne sound. If necessary, acoustic FEA analyses are supplemented by vibroacoustic measurements in order to achieve the most meaningful and reliable results possible. You too can benefit from our many years of experience in processing and solving acoustic problems, e.g. in machine acoustics or vehicle acoustics.
Acoustic simulations and acoustic measurements therefore play an important role in many industries. Acoustic analyses are an effective means of counteracting unnecessary or excessive noise development. An FEA acoustic analysis helps you to understand the sound emissions of your products and to reduce them in a targeted manner. We simulate and optimize the sound emission of your products using FEA simulation, taking into account fluid-structure coupling, the interaction of airborne sound and structure-borne sound. If necessary, acoustic FEA analyses are supplemented by vibroacoustic measurements in order to achieve the most meaningful and reliable results possible. You too can benefit from our many years of experience in processing and solving acoustic problems, e.g. in machine acoustics or vehicle acoustics.
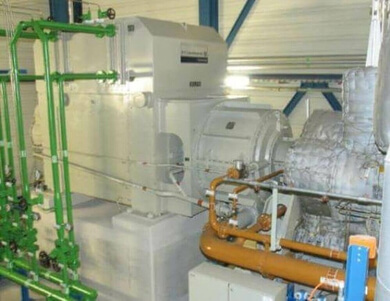
learn more
Thermal FEA analysis
We carry out thermal simulations / thermal analyses on the basis of FEA analyses in order to simulate the effects of thermal loads. Our thermal analyses provide precise predictions of temperature curves, temperature gradients, cooling behavior and heating behavior of your components, assemblies, and systems. In addition to diverse types of thermal loads, we take into account thermal conduction, thermal radiation and convection for both stationary and transient thermal systems. The free and forced convection can either be specified using correlation coefficients or determined using a CFD simulation coupled with the thermal system.
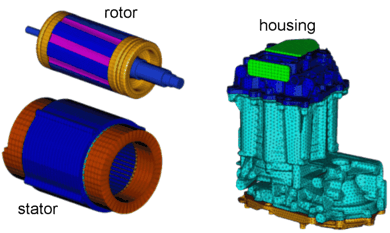
learn morePDF
CFD simulation / flow simulation
We use flow simulations or CFD analyses (CFD = Computational Fluid Dynamics) to investigate flow around or through systems. We offer you fluid simulations, if necessary, also coupled with thermal simulations for a variety of fluid dynamic tasks. Input variables can be, for example, inflow or outflow velocities, mass and volume flows or pressure differences as well as thermal boundary conditions such as heat loads or surface temperatures. Depending on the application, we determine the hydrodynamics, flow dynamics, thermodynamics and fluid dynamics of your system and thus provide you with effective support in optimizing your products.
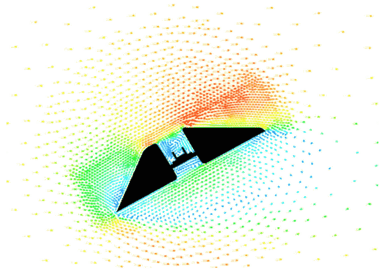
learn morePDF
Free Consultation
Our specialists are always at your disposal to flexibly respond to your respective requirements and wishes.
Dr. Michael Elbs, Managing Director
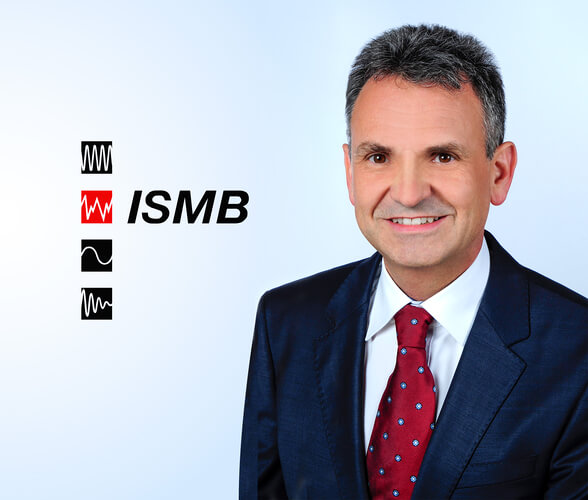
FEA simulation explained
What does FEA mean?
FEA stands for “Finite Element Analysis” and refers to a series of numerical methods for solving various physical problems. Components, assemblies, and systems are virtually simulated and subjected to predefined influences. In this way, for example, strength and deformation analyses, vibration analyses, thermal analyses, flow simulations, electromagnetic simulations and even weather forecasts can be carried out.
The name of the finite element method comes from the fact that real, even very complex geometric structures are approximated by a countable number of geometrically simple partial shapes, e.g. cuboids or tetrahedrons, using so-called finite elements. The modeling, solution methods and presentation of results of FEA models have been continuously developed and improved over the last few decades. Together with the constant increase in computer performance, this has led to FEA analyses becoming a standard simulation tool in many areas of technology and science.
The name of the finite element method comes from the fact that real, even very complex geometric structures are approximated by a countable number of geometrically simple partial shapes, e.g. cuboids or tetrahedrons, using so-called finite elements. The modeling, solution methods and presentation of results of FEA models have been continuously developed and improved over the last few decades. Together with the constant increase in computer performance, this has led to FEA analyses becoming a standard simulation tool in many areas of technology and science.